فرآیند نورد و دستگاه آن
نورد (rolling) مهمترین فرآیند تولید مقاطع فولادی است. در این فرآیند با اعمال فشار، سایز و شکل مقاطع فولادی تغییر پیدا میکند. وظیفه اعمال این فشار و شکلدهی شمش به ورق، تغییر ابعاد و ضخامت ورق و… بر عهده دستگاه نورد یا نورد رولینگ است. وجود این دستگاه برای صنایع بسیاری حیاتی و ضروری است. اگر شما هم به این دستگاه نیاز دارید یا علاقه دارید بیشتر در مورد دستگاه نورد ورق بدانید با ما در این مطلب همراه باشید. در ادامه قصد داریم این دستگاه را بهطور کامل بررسی کنیم.
نورد ورق و انواع آن
احتمالا اولین سوالی که وجود دارد این است که اصلا نورد ورق چیست؟ نورد ورق یا رولینگ روشی است که برای نازکتر کردن یا شکلدهی به ورق فولادی استفاده میشود. نورد ورق بدون ایجاد تغییر در عرض ورق باعث تغییر ضخامت و افزایش طول آن میشود. همچنین از این روش برای تبدیل ورق به مقاطع گرد و منحنی استفاده میشود. بهطور مثال، محصولاتی مانند تیرآهن و نبشی با همین روش تولید میشوند. این فرآیند به دو روش گرم و سرد انجام میشود که تفاوتهای قابل ملاحظهای را با هم دارند.
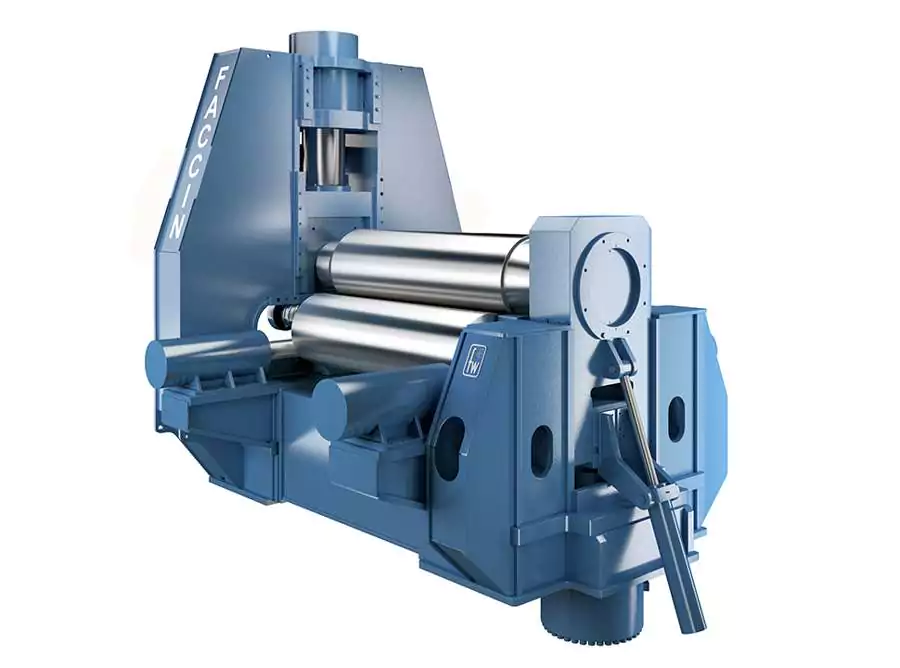
نورد سرد ورق
منظور از نورد سرد عملیاتی است که در دمای محیط انجام میشود. فرآیند نورد سرد کمی پیچیده است و هدف از انجام عملیات نورد سرد تولید یک ورق فولادی صیقلی و صاف با مقاومت بالا و ضخامت پایین است. این فرآیند موجب افزایش استحکام و رفع ترکهای سطحی ورق میشود. برای این فرآیند ابتدا ورق تحت عملیات آنیل قرار میگیرد تا پسماندهای آن از بین برود. پروفیل سبک یکی از مقاطع فولادی است که از نورد سرد و با ورق روغنی تولید میشود.
محصولات گرم قبل از این فرآیند باید اسیدشویی شوند تا از آسیبدیدن غلطکها به دلیل زبری سطح آنها جلوگیری شود. ورق تولیدشده در این فرآیند را با نامهای ورق سرد یا ورق روغنی میشناسید. عموما پس از این فرآیند و از آنجایی که سطح صاف این ورقها آماده پوششدهی است، عملیات گالوانیزاسیون انجام میشود. ورق گالوانیزه که حاصل این عملیات است در برابر رطوبت، خوردگی و زنگزدگی مقاوم است.
این ورق برای استفاده در صنایع مختلف و در معرض رطوبت یک انتخاب مناسب خواهد بود. بنابراین، عملیات نورد سرد برای کاهش ضخامت، تغییر شکل و ابعاد و ازبینرفتن نقطه تسلیم استفاده میشود. در یک تعریف دقیقتر، رولهایی که در عملیات نورد گرم که در ادامه به آن خواهیم پرداخت تولید میشوند، پس از اسیدشویی توسط عملیات نورد سرد در معرض کاهش ضخامت و تغییر شکل قرار میگیرند.
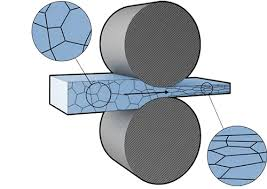
نورد گرم ورق
نورد گرم یکی دیگر از انواع این عملیات است که باعث شکلپذیری و استحکام بیشتر محصول میشود. در این عملیات، ابتدا فولاد را به میزان لازم حرارت میدهند؛ سپس آن را از کوره خارج میکنند و برای نورد به قسمت غلطکها میفرستند. در این قسمت عموما سه بار از غلطکهای سنگین و 6 الی 7 بار از غلطکهای سبکتر استفاده میشود. در این فرآیند طول فلز افزایش پیدا میکند و ضخامت آن کم میشود. همچنین باید بدانید، مقاطعی که در نورد گرم تولید میشوند، استحکام بالاتری نسبت به قطعاتی دارند که در نورد سرد تولید میشوند.
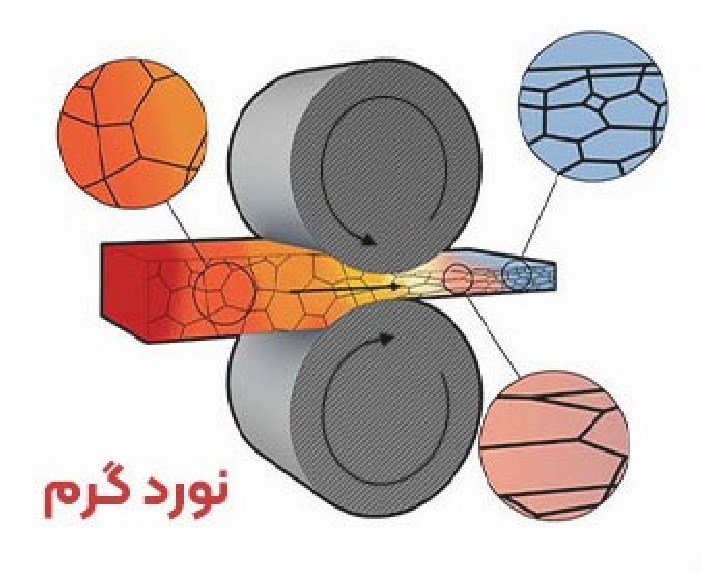
این فرآیند سبب تولید ورق سیاه میشود که دارای سطحی زبر و رنگی کدر است. مهمترین ویژگیهای این محصول استحکام بالا، گریدهای مختلف، امکان استفاده در صنایع عظیم و گسترده، استفاده بهعنوان ماده اولیه تولید سایر ورقها و نرخ مقرونبهصرفه است. عملیات نورد گرم چند مزیت مهم دارد:
- تجهیزات مورد نیاز برای عملیات نورد گرم کمتر از روش نورد سرد است.
- قطعات تولیدشده در فرآیند نورد گرم به پردازش کمتری نیاز دارند؛ به همین دلیل، این قطعات هزینه کمتری نسبت به قطعات نورد سرد دارند.
- نورد گرم مناسبترین روش برای تولید شمشهای بزرگ است.
- سردکردن محصولات بهدست آمده از فرآیند نورد گرم با دمای مناسب انجام میشود. همین موضوع باعث میشود تا از خشک یا سختشدن این قطعات جلوگیری شود.
- برای تغییر شکل قطعاتی که از نورد گرم بهدست میآیند، انرژی کمتری احتیاج است.
تاریخچه دستگاههای نورد: مرور بر توسعه تاریخی این دستگاهها
شاید نتوان تاریخ دقیقی را برای اختراع دستگاههای نورد مشخص کرد. اما شواهد نشان میدهد که انسانها از زمانهای بسیار دور از روشهای ابتدایی برای شکلدهی فلزات استفاده میکردهاند. در ابتدا، از ابزارهای دستی سادهای مانند چکش و سندان برای تغییر شکل فلزات استفاده میشد. با گذشت زمان، نیاز به تولید قطعات فلزی با دقت و حجم بالاتر، انسانها را به سمت ابداع روشهای جدید سوق داد.
انقلاب صنعتی و پیشرفت نورد
با شروع انقلاب صنعتی در قرن ۱۸ و ۱۹، نیاز به تولید انبوه محصولات فلزی به شدت افزایش یافت. این امر باعث شد تا دستگاههای نورد به صورت مکانیکی و با بهرهگیری از نیروی آب و بخار توسعه یابند. در این دوره، دستگاههای نورد سادهای ساخته شدند که میتوانستند شمشهای فلزی را به ورقها و مقاطع ساده تبدیل کنند.
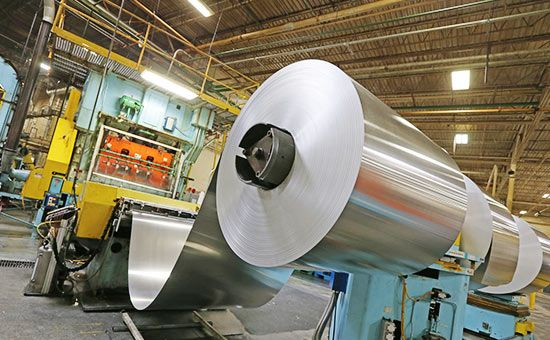
قرن بیستم و عصر طلایی نورد
قرن بیستم، عصر طلایی برای توسعه دستگاههای نورد بود. با پیشرفت فناوری و درک بهتر خواص مواد، دستگاههای نورد پیچیدهتر و کارآمدتری ساخته شدند. برخی از مهمترین تحولات این دوره عبارتند از:
- نورد سرد: در این روش، فلزات در دمای محیط یا دمای پایین نورد میشوند که باعث افزایش دقت ابعاد و بهبود خواص مکانیکی محصول میشود.
- نورد گرم: در این روش، فلزات در دمای بالا نورد میشوند که باعث کاهش نیروی مورد نیاز برای شکلدهی و افزایش سرعت تولید میشود.
- نورد چند مرحلهای: در این روش، فلزات در چندین مرحله و با استفاده از غلتکهای مختلف نورد میشوند تا به شکل نهایی مورد نظر برسند.
- نورد پیوسته: در این روش، فلز به صورت پیوسته از بین غلتکها عبور میکند که باعث افزایش سرعت تولید و کاهش هزینهها میشود.
عصر حاضر و آینده نورد
امروزه، دستگاههای نورد به یکی از پیشرفتهترین تجهیزات صنعتی تبدیل شدهاند. با استفاده از نرمافزارهای پیشرفته، میتوان فرآیند نورد را شبیهسازی کرده و بهینه کرد. همچنین، از حسگرها و سیستمهای کنترل هوشمند برای نظارت بر فرآیند نورد و اطمینان از کیفیت محصول استفاده میشود.
در آینده، انتظار میرود که دستگاههای نورد با استفاده از فناوریهای نوینی مانند هوش مصنوعی، یادگیری ماشین و چاپ سهبعدی، تحولات چشمگیری را تجربه کنند. این فناوریها میتوانند به تولید قطعات فلزی با پیچیدگی بالا و در مقیاس کوچک کمک کنند و همچنین باعث کاهش مصرف انرژی و مواد اولیه شوند.
تاریخچه دستگاههای نورد، حکایت از تلاش انسان برای تسلط بر فلزات و شکلدهی آنها به اشکال مختلف است. از ابزارهای دستی ساده تا دستگاههای پیچیده امروزی، این دستگاهها همواره در حال تکامل بودهاند و نقش مهمی در پیشرفت تمدن بشری ایفا کردهاند.
آشنایی با انواع دستگاه نورد ورق
هرکدام از انواع نورد ورق، خصوصیات و مزایا و معایب خاص خود را دارند. همچنین محصولاتی که از این عملیات خارج میشوند در صنایع مختلف و کاربردهای گوناگونی بهکار میروند. در ادامه به معرفی انواع دستگاه نورد ورق میپردازیم. عملیات حرارتی و انواع نورد به بهبود خواص محصولات فلزی منجر میشوند و در کل این عملیات روی قیمت و کیفیت مقاطع فولادی هم تاثیرگذار هستند.
نورد ورق پیچ
فرآیند انجام این نورد به این صورت است که میلهای را از روی دو صفحه که حالت تخت دارند، عبور میدهند. روی این صفحات، شیار پیچ وجود دارد؛ به همین دلیل هم میتواند با سرعت و کیفیت بالا پیچ تولید کند.
نورد ورق حلقه
در این فرآیند ماده بین دو غلطک داخلی و خارجی قرار میگیرد و فشاری که از دو غلطک به آن وارد میشود، سبب کاهش ضخامت و افزایش شعاع این ماده میشود.
نورد ورق تیرآهن
هدف از انجام فرآیند نورد ورق تیرآهن رسیدن به ابعاد دلخواه است. در این فرآیند ابتدا شمش فولادی را در کورههای نورد ورق قرار میدهند. سپس ماده بهدست آمده از این کورهها را از قفسههای غلطکی عبور میدهند تا در نهایت این شمش دچار تغییر شکل شود. تیرآهنی که با عملیات نورد گرم تولید میشود، انعطاف بسیار خوبی خواهد داشت. به همین دلیل از این تیرآهن بهصورت گسترده در ساختمانسازی استفاده میشود. همچنین تیرآهنی که در فرآیند نورد سرد تولید میشود، بهدلیل دوام بالایی که دارد در سازههایی استفاده میشود که به تحمل بالا نیاز دارند. این تیرآهن در کنار پروفیل قوطی آهن از بیشترین مقاطعی هستند که در صنعت ساختمان کاربرد دارند.
نورد ورق آلومینیومی
در این نوع از نورد ورق هم مانند سایر روشها ورق آلومینیومی از میان غلطکها عبور داده میشود. این فرآیند هم بهدلیل وجود غلطکها درواقع باعث کاهش ضخامت و افزایش طول محصول میشود. دستگاه نورد ورق شامل اجزای مختلفی مانند غلطک، قفسه، یاتاقان و محفظه نگهداری از قطعات است. گاهی برای ایجاد ورق از نورد دو غلطکی استفاده میشود. در این روش دو غلطک در جهت مخالف هم حرکت میکنند و همین امر باعث کاهش ضخامت ورق مورد نظر میشود.
نکات ایمنی در استفاده از دستگاه نورد: راهکارهای جلوگیری از حوادث
دستگاههای نورد به دلیل قدرت و سرعت بالایی که دارند، پتانسیل ایجاد حوادث جدی را دارند. رعایت نکات ایمنی در حین کار با این دستگاهها بسیار ضروری است. در ادامه به برخی از مهمترین نکات ایمنی اشاره میشود:
قبل از شروع کار:
- آموزش کامل: تمامی اپراتورها باید آموزشهای لازم در مورد نحوه کار با دستگاه، خطرات احتمالی و اقدامات ایمنی را دیده باشند.
- بازرسی دستگاه: قبل از هر شیفت کاری، تمامی قسمتهای دستگاه به ویژه غلتکها، سیستم هیدرولیک و سیستم کنترل باید به دقت بررسی شوند تا از سلامت آنها اطمینان حاصل شود.
- لباس کار مناسب: استفاده از لباس کار مناسب، کفش ایمنی، دستکش و عینک ایمنی الزامی است.
- حذف اشیاء اضافی: تمامی اشیاء اضافی مانند ابزارآلات، جواهرات و ساعت باید از دست و بدن اپراتور دور نگه داشته شوند.
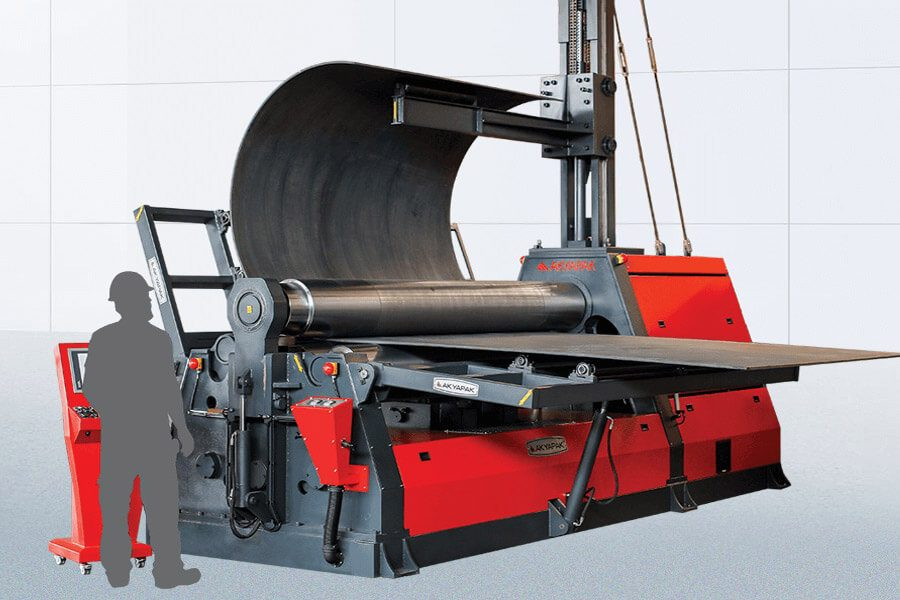
حین کار:
- تمرکز کامل: اپراتور باید در طول کار تمرکز کامل داشته باشد و از انجام کارهای جانبی خودداری کند.
- رعایت فاصله ایمنی: هیچگاه دست یا بدن را نزدیک قسمتهای متحرک دستگاه نبرید.
- استفاده از ابزارهای مناسب: برای برداشتن مواد از ابزارهای مناسب استفاده کنید و از دست خالی استفاده نکنید.
- کنترل سرعت: سرعت دستگاه را متناسب با نوع کار و جنس مواد تنظیم کنید.
- توقف اضطراری: در صورت بروز هرگونه مشکل یا خطر، بلافاصله دستگاه را متوقف کنید.
نکات ایمنی عمومی:
- تعمیر و نگهداری: دستگاه به صورت دورهای باید سرویس و تعمیر شود.
- سیستم تهویه مناسب: محیط کار باید دارای سیستم تهویه مناسب باشد تا از تجمع گرد و غبار و بخارات مضر جلوگیری شود.
- آشنایی با سیستم اطفاء حریق: تمامی افراد باید با نحوه استفاده از تجهیزات اطفاء حریق آشنا باشند.
- برقگیر: دستگاه باید به سیستم برقگیر مناسب متصل باشد.
خطرات احتمالی و راهکارهای مقابله با آنها:
- گیر کردن دست یا پا: استفاده از حفاظهای ایمنی، آموزش صحیح و رعایت فاصله ایمنی.
- برقگرفتگی: استفاده از سیمهای ارت، بررسی دورهای عایقبندی سیمها و تجهیزات.
- آتشسوزی: استفاده از مواد اشتعالناپذیر، وجود سیستم اطفاء حریق مناسب و آموزش افراد.
- پرتاب قطعات: استفاده از حفاظهای ایمنی، تعمیر به موقع دستگاه و بررسی تعادل دستگاه.
کاربردهای مختلف دستگاه نورد ورق در صنایع مختلف
شاید برای شما هم این سوال پیش آمده که دستگاه نورد ورق که تا اینجا به آن پرداختیم، در صنایع مختلف چه کاربردی دارد. این دستگاه بیشتر برای ساخت مقاطع مسطح یا طویل، مقاطع گرد و منحنی و همچنین مقاطع مربعی، مستطیلی و… استفاده میشود. این مقاطع در واقع ماده اولیه تولید در صنایع مختلف هستند. هر کدام از این تجهیزات براساس ویژگیهایی که دارند، بهعنوان مواد اولیه برای تولیدات مختلف در صنایع گوناگون استفاده میشوند. انجام عملیات نورد سرد و نورد گرم هم باعث ایجاد تفاوتهایی در خصوصیات ظاهری، خواص، ویژگیها و ساختار این محصولات میشوند. کاربردهای مختلف دستگاه نورد ورق در صنایع مختلف عبارتند از:
- تولید تیرآهن و میلگرد برای صنعت ساختمانسازی
- تولید قطعات مختلف مانند قطعات موتور، یاتاقان، شاتون، قاب شاسی و سیستم تعلیق و.. برای صنایع خودروسازی
- تولید ریلهای مختلف و قطعات واگن و.. در راهآهن
- ساخت انواع تجهیزات صنعتی مانند نوار نقاله در صنایع ماشینآلات
- ساخت انواع تهویه مطبوع برای تولید چیلر، انواع فنکویل، داکت اسپلیت و…
- لولهسازی برای انتقال سیالات، آب، نفت، گاز و… در صنعت نفت، گاز و…
انواع عملیات نورد
عملیات نورد با عبور فلزات از بین غلطکهای مخصوص استوانهای انجام میشود. این غلطکها در خلاف جهت هم قرار گرفته و بهصورت رفت و برگشتی و با برسهای مخصوص روی سطح محصولات حرکت میکنند. از طرفی این غلطکها در برخی موارد برای سردکاری یا گرمکاری بعضی از انواع فلزات هم استفاده میشوند. با اینحال عملیات نورد شامل انواع مختلفی است که برخی از آنها عبارتند از:
- عملیات نورد معمول: از این عملیات برای افزایش میزان تختی قطعه استفاده میشود.
- نورد عرضی: این عملیات برای مقاطع دارای تقارن استفاده میشود.
- عملیات نورد حلقه: برای کاهش حجم و افزایش شعاع از این عملیات استفاده میشود که در آن غلطک داخلی و غلطک خارجی فشاری را روی یک حلقه وارد میکنند.
- عملیات نورد چندلایه:در این روش چند لایه فلز با همدیگر در فرآیند نورد قرار میگیرند.
- نورد پیچ: در این فرآیند میله از بین دو صفحه تخت یا شیارهای پیچ عبور میکند و پیچ با کیفیت بالا و سرعت تولید میشود.
نحوه انتخاب دستگاه نورد مناسب برای صنایع مختلف: براساس نیاز و مشخصات فنی
یکی از کلیدیترین تصمیمات در فرآیند تولید محصولات فلزی، انتخاب دستگاه نورد مناسب است. چرا که انتخاب نادرست دستگاه نورد میتواند به کاهش کیفیت محصول، افزایش هزینهها و کاهش بهرهوری منجر شود. بنابراین، درک دقیق از نیازها و مشخصات فنی دستگاه نورد، برای اتخاذ تصمیم صحیح، ضروری است.
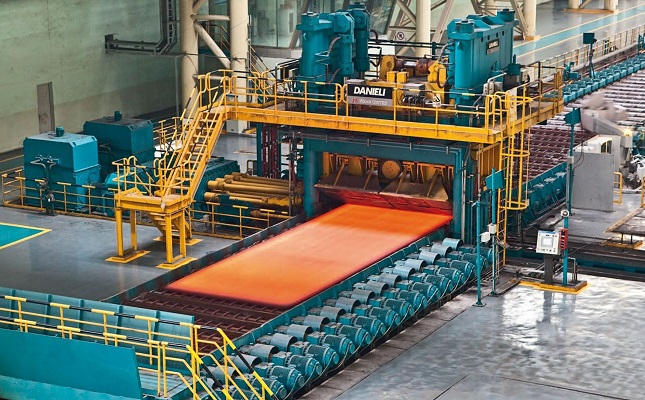
عوامل موثر در انتخاب دستگاه نورد
عوامل متعددی در انتخاب دستگاه نورد مناسب نقش دارند که برخی از مهمترین آنها عبارتند از:
- نوع محصول نهایی:
- ورق: برای تولید ورقهای فلزی با ضخامت و عرض مختلف، دستگاههای نورد سرد و گرم مورد استفاده قرار میگیرند.
- پروفیل: برای تولید پروفیلهای ساختمانی، صنعتی و تزئینی، از دستگاههای نورد مخصوص پروفیل استفاده میشود.
- لوله: دستگاههای نورد لوله برای تولید لولههای فولادی، آلومینیومی و مسی به کار میروند.
- جنس ماده اولیه: نوع فلزی که قرار است نورد شود (فولاد، آلومینیوم، مس و …) بر انتخاب دستگاه و تنظیمات آن تاثیرگذار است.
- ابعاد محصول نهایی: ضخامت، عرض و طول محصول نهایی، ظرفیت دستگاه را تعیین میکند.
- دقت ابعادی: برای تولید محصولات با دقت ابعادی بالا، دستگاههای نورد با سیستم کنترل دقیق مورد نیاز است.
- ظرفیت تولید: میزان تولید مورد نیاز در واحد زمان، بر انتخاب دستگاه با ظرفیت مناسب تاثیرگذار است.
- بودجه: هزینه خرید، نصب و راهاندازی دستگاه، یکی از عوامل مهم در انتخاب است.
مشخصات فنی مهم یک دستگاه نورد
نوع سیستم نورد | دو غلتکی، سه غلتکی، چهار غلتکی و … |
تعداد پاس نورد | تعداد پاسهایی که ورق از بین غلتکها عبور میکند |
قطر غلتکها | قطر غلتکها بر روی ضخامت ورق خروجی تاثیرگذار است |
عرض کاری | حداکثر عرض ورقی که دستگاه میتواند نورد کند |
قدرت موتور | قدرت موتور دستگاه بر روی ظرفیت تولید تاثیرگذار است |
سیستم کنترل | سیستم کنترل دستگاه میتواند دستی، نیمه اتوماتیک یا تمام اتوماتیک باشد |
مراحل انتخاب دستگاه نورد
- تعیین نیازها: به طور دقیق مشخص کنید که چه محصولی با چه ابعادی و با چه ظرفیتی نیاز دارید.
- مقایسه دستگاههای مختلف: مشخصات فنی دستگاههای مختلف را با یکدیگر مقایسه کنید و دستگاهی را انتخاب کنید که بیشترین تطابق را با نیازهای شما داشته باشد.
- مشاوره با کارشناسان: از کارشناسان متخصص در زمینه دستگاههای نورد کمک بگیرید تا بهترین انتخاب را داشته باشید.
- بازدید از کارخانه سازنده: در صورت امکان، از کارخانه سازنده دستگاه بازدید کنید تا از کیفیت ساخت و عملکرد دستگاه اطمینان حاصل کنید.
مقایسه دستگاههای نورد دستی و اتوماتیک: مزایا و معایب هرکدام
دستگاههای نورد، چه دستی و چه اتوماتیک، نقش مهمی در شکلدهی فلزات ایفا میکنند. هر کدام از این دستگاهها، مزایا و معایبی دارند که انتخاب مناسبترین نوع، به نیازهای خاص تولید بستگی دارد.
دستگاههای نورد دستی
دستگاه نورد دستی ابزاری است که با استفاده از نیروی دست، فلزات را نازکتر و پهنتر میکند. این دستگاهها مزایا و معایبی دارند که در ادامه آنها را بررسی میکنیم:
مزایا | معایب |
سادگی و هزینه کم | سرعت پایین |
انعطافپذیری بالا | دقت پایین |
عدم نیاز به نیروی کار متخصص | خستگی اپراتور |
احتمال بروز خطای انسانی | |
نیاز به نیروی کار بیشتر |
دستگاههای نورد اتوماتیک
دستگاههای نورد اتوماتیک، ماشینآلات صنعتی پیشرفتهای هستند که به صورت خودکار و با دقت بالا، فلزات را به ورق، پروفیل و سایر مقاطع مورد نظر تبدیل میکنند. این دستگاهها به دلیل بهرهگیری از سیستمهای کنترل عددی (CNC) و هیدرولیک، قادر به انجام عملیات نورد با سرعت و دقت بسیار بالا هستند و در صنایع مختلفی همچون خودروسازی، ساختمانی و الکترونیک کاربرد گستردهای دارند. این دستگاهها مزایا و معایبی را شامل میشوند که در ادامه به بررسی آنها میپردازیم.
مزایا | معایب |
سرعت بالا | هزینه بالا |
دقت بالا | پیچیدگی |
کیفیت یکنواخت | انعطافپذیری پایین |
کاهش نیروی انسانی | وابستگی به برق |
امکان برنامهریزی |
چه زمانی از دستگاه نورد دستی و چه زمانی از دستگاه نورد اتوماتیک استفاده کنیم؟
- دستگاههای نورد دستی: برای تولید قطعات با تیراژ پایین، قطعات با ابعاد و شکلهای خاص، و در مواردی که هزینه اولیه مهمترین عامل است مناسب هستند.
- دستگاههای نورد اتوماتیک: برای تولید انبوه محصولات با دقت بالا و کیفیت یکنواخت، در صنایع بزرگ و برای کاهش هزینههای تولید در بلندمدت مناسب هستند.
بهرهوری انرژی در دستگاههای نورد: راهکارهای کاهش مصرف انرژی
دستگاههای نورد به عنوان مصرفکنندههای بزرگ انرژی در صنایع فلزی شناخته میشوند. کاهش مصرف انرژی در این دستگاهها نه تنها به صرفهجویی در هزینهها کمک میکند بلکه به کاهش اثرات زیستمحیطی نیز میانجامد. در ادامه به برخی از راهکارهای کاهش مصرف انرژی در دستگاههای نورد اشاره میشود:
1. بهینهسازی فرآیند نورد:
- کاهش تعداد پاسهای نورد: با بهینهسازی طراحی غلتکها و تنظیمات فرآیند، میتوان تعداد پاسهای مورد نیاز برای رسیدن به ضخامت نهایی را کاهش داد.
- کنترل دقیق ضخامت: با استفاده از سیستمهای کنترل دقیق ضخامت، میتوان از نورد بیش از حد فلز جلوگیری کرد.
- کاهش نیروی نورد: با استفاده از روانکارهای مناسب و طراحی بهینه غلتکها میتوان نیروی مورد نیاز برای نورد را کاهش داد.
2. استفاده از موتورهای با راندمان بالا:
- موتورهای الکتریکی با راندمان بالا: استفاده از موتورهای الکتریکی با راندمان بالا و تکنولوژیهای نوین مانند موتورهای القایی با روتور قفس سنجابی و موتورهای سنکرون آهنربای دائم میتواند به کاهش مصرف انرژی کمک کند.
- درایوهای فرکانس متغیر: استفاده از درایوهای فرکانس متغیر برای کنترل سرعت موتورها، باعث کاهش مصرف انرژی و افزایش دقت کنترل فرآیند میشود.
3. بهبود سیستمهای حرارتی:
- عایقبندی مناسب: عایقبندی مناسب کورهها و سایر تجهیزات گرمایشی میتواند از اتلاف حرارت جلوگیری کند.
- بازیافت حرارت: بازیافت حرارت از سیالات خروجی کورهها و سایر تجهیزات میتواند برای پیش گرم کردن مواد اولیه استفاده شود.
4. استفاده از روانکارهای مناسب:
- روانکارهای با ویسکوزیته پایین: استفاده از روانکارهای با ویسکوزیته پایین میتواند به کاهش اصطکاک و در نتیجه کاهش مصرف انرژی کمک کند.
- روانکاری دقیق: روانکاری دقیق و به موقع تجهیزات میتواند از سایش و پارگی قطعات جلوگیری کرده و عمر مفید آنها را افزایش دهد.
5. سیستمهای کنترل پیشرفته:
- سیستمهای کنترل هوشمند: استفاده از سیستمهای کنترل هوشمند و مبتنی بر هوش مصنوعی میتواند به بهینهسازی فرآیند نورد و کاهش مصرف انرژی کمک کند.
- پایش مداوم مصرف انرژی: با استفاده از سنسورها و نرمافزارهای مناسب میتوان مصرف انرژی را به صورت مداوم پایش کرده و نقاط ضعف را شناسایی کرد.
6. توجه به طراحی کارخانه:
- چیدمان مناسب تجهیزات: چیدمان مناسب تجهیزات و به حداقل رساندن مسافت پیمایش مواد اولیه میتواند به کاهش مصرف انرژی کمک کند.
- استفاده از تجهیزات حملونقل کارآمد: استفاده از تجهیزات حملونقل کارآمد مانند جرثقیلها و نوار نقالهها میتواند به کاهش مصرف انرژی کمک کند.
7. آموزش پرسنل:
- آموزش پرسنل: آموزش پرسنل در مورد اهمیت صرفهجویی در انرژی و روشهای کاهش مصرف انرژی میتواند به فرهنگسازی در این زمینه کمک کند.
با اجرای این راهکارها، میتوان به طور قابل توجهی مصرف انرژی در دستگاههای نورد را کاهش داده و به بهبود بهرهوری انرژی در صنایع فلزی کمک کرد.
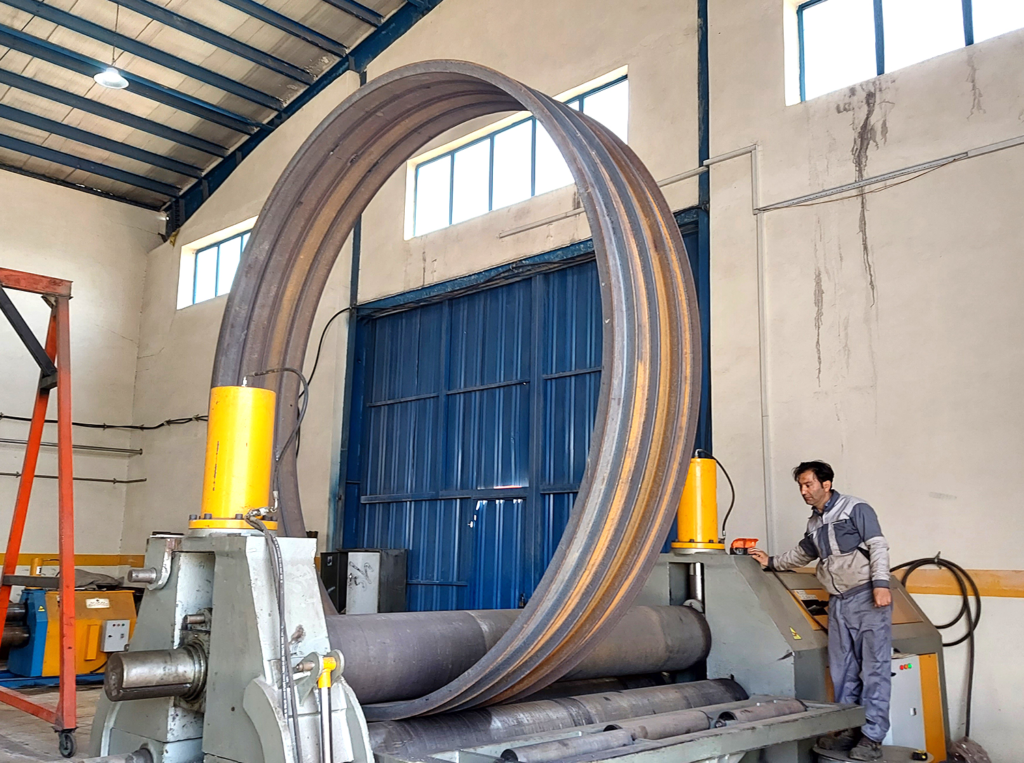
بررسی دستگاههای نورد جدید و نوآوریها در این زمینه
صنعت نورد همواره در حال تحول و پیشرفت است و دستگاههای نورد جدید با بهرهگیری از فناوریهای نوین، تواناییهای تولید را به طور چشمگیری افزایش دادهاند. در ادامه به برخی از مهمترین نوآوریها و ویژگیهای دستگاههای نورد جدید میپردازیم:
نوآوریهای کلیدی در دستگاههای نورد جدید:
- سیستمهای کنترل پیشرفته:
- CNC پیشرفته: استفاده از سیستمهای کنترل عددی با دقت بالا (CNC) امکان برنامهریزی و اجرای فرآیندهای پیچیده نورد را با دقت بسیار بالا فراهم میکند.
- سیستمهای کنترل تطبیقی: این سیستمها با پایش مداوم پارامترهای فرآیند، تنظیمات دستگاه را به صورت خودکار بهینه میکنند تا کیفیت محصول نهایی افزایش یابد.
- مواد جدید برای غلتکها:
- آلیاژهای مقاوم به سایش: استفاده از آلیاژهای جدید و مقاوم به سایش برای ساخت غلتکها، عمر مفید آنها را افزایش داده و کیفیت سطح محصول نهایی را بهبود میبخشد.
- پوششهای سخت: پوششدهی غلتکها با مواد سخت و مقاوم به حرارت، از جمله پوششهای الماسهای و سرامیکی، مقاومت آنها در برابر سایش و خوردگی را افزایش میدهد.
- سیستمهای روانکاری پیشرفته:
- روانکارهای هوشمند: استفاده از روانکارهای هوشمند که با توجه به شرایط کاری، میزان و نوع روانکاری را تنظیم میکنند، به کاهش مصرف روانکار و افزایش عمر مفید تجهیزات کمک میکند.
- سیستمهای اندازهگیری دقیق:
- سنسورهای لیزری و نوری: استفاده از سنسورهای لیزری و نوری برای اندازهگیری دقیق ضخامت و عرض ورق، به کنترل بهتر فرآیند نورد و بهبود کیفیت محصول کمک میکند.
- سیستمهای اتوماسیون صنعتی:
- رباتهای صنعتی: استفاده از رباتهای صنعتی برای انجام عملیات بارگذاری و تخلیه مواد اولیه و محصولات نهایی، به افزایش بهرهوری و کاهش هزینههای تولید کمک میکند.
- سیستمهای بینایی ماشین: استفاده از سیستمهای بینایی ماشین برای بازرسی و کنترل کیفیت محصولات نهایی، به افزایش دقت و اطمینان از کیفیت محصولات کمک میکند.
مزایای دستگاههای نورد جدید:
- افزایش دقت و کیفیت محصولات: با استفاده از سیستمهای کنترل دقیق و مواد جدید، میتوان محصولاتی با کیفیت و دقت ابعادی بسیار بالا تولید کرد.
- افزایش بهرهوری: اتوماسیون فرآیندهای نورد، کاهش نیروی کار و افزایش سرعت تولید را به دنبال دارد.
- کاهش مصرف انرژی: استفاده از موتورهای با راندمان بالا، سیستمهای کنترل هوشمند و سایر فناوریهای نوین، به کاهش مصرف انرژی و هزینههای تولید کمک میکند.
- کاهش ضایعات: با کنترل دقیق فرآیند نورد و کاهش خطاهای انسانی، میتوان میزان ضایعات را به حداقل رساند.
- انعطافپذیری بیشتر: دستگاههای نورد جدید قادر به تولید طیف وسیعی از محصولات با ابعاد و مشخصات مختلف هستند.
کاربردهای دستگاههای نورد جدید:
دستگاههای نورد جدید در صنایع مختلفی از جمله خودروسازی، ساختمانی، بستهبندی، الکترونیک و هوافضا کاربرد گستردهای دارند. از این دستگاهها برای تولید ورقهای فلزی، پروفیلها، لولهها و سایر محصولات فلزی استفاده میشود.
مشکلات رایج در دستگاههای نورد و نحوه رفع آنها
دستگاههای نورد به عنوان قلب تپنده بسیاری از صنایع فلزی، ممکن است در طول زمان با مشکلاتی مواجه شوند که بر عملکرد و کیفیت محصول نهایی تاثیر میگذارد. در این بخش به برخی از مشکلات رایج در دستگاههای نورد و راهکارهای رفع آنها میپردازیم:
مشکلات مربوط به غلتکها
- سایش غلتکها: سایش غلتکها یکی از مشکلات رایج است که منجر به کاهش دقت ابعادی و کیفیت سطح محصول میشود.
- راه حل: استفاده از آلیاژهای مقاوم به سایش برای ساخت غلتکها، پوششدهی غلتکها با مواد سخت و مقاوم به سایش، روانکاری مناسب و تنظیم دقیق نیروی نورد.
- شکستگی غلتکها: شکستگی غلتکها معمولاً به دلیل اضافه بار، عیوب ساختاری یا نصب نامناسب رخ میدهد.
- راه حل: بازرسی منظم غلتکها، تعویض به موقع غلتکهای معیوب، تنظیم دقیق نیروی نورد و جلوگیری از اضافه بار.
- لرزش غلتکها: لرزش غلتکها میتواند به دلیل عدم تعادل، سایش یاتاقانها یا شل شدن پیچها رخ دهد.
- راه حل: بالانس کردن غلتکها، تعویض یاتاقانهای معیوب، محکم کردن پیچها و تنظیم دقیق سیستم هدایت غلتکها.
مشکلات مربوط به سیستمهای هیدرولیک
- نشت روغن: نشت روغن از اتصالات و سیلندرهای هیدرولیک میتواند منجر به کاهش فشار روغن و اختلال در عملکرد دستگاه شود.
- راه حل: تعویض واشرهای فرسوده، محکم کردن اتصالات و بررسی منظم سیستم هیدرولیک به منظور تشخیص و رفع نشتیها.
- کاهش فشار روغن: کاهش فشار روغن میتواند به دلیل نشتی روغن، آلودگی روغن یا خرابی پمپ روغن رخ دهد.
- راه حل: بررسی سیستم هیدرولیک به منظور تشخیص و رفع نشتیها، تعویض روغن آلوده، تعمیر یا تعویض پمپ روغن.
مشکلات مربوط به سیستمهای الکتریکی
- قطع مداوم برق: قطع مداوم برق میتواند به دلیل مشکلات در مدارهای الکتریکی، خرابی کنتاکتورها یا سوئیچها رخ دهد.
- راه حل: بررسی و تعمیر مدارهای الکتریکی، تعویض قطعات معیوب و استفاده از تجهیزات حفاظتی مناسب.
- گرم شدن بیش از حد موتورها: گرم شدن بیش از حد موتورها میتواند به دلیل اضافه بار، نقص در سیستم خنککاری یا اتصال کوتاه رخ دهد.
- راه حل: بررسی و تنظیم بار موتور، بررسی سیستم خنککاری و تعمیر یا تعویض قطعات معیوب.
مشکلات مربوط به سیستمهای کنترل
- اختلال در عملکرد سیستم کنترل: اختلال در عملکرد سیستم کنترل میتواند به دلیل خرابی سنسورها، خرابی بردهای الکترونیکی یا نرمافزاری رخ دهد.
- راه حل: بررسی و تعمیر سنسورها، تعویض بردهای الکترونیکی معیوب و بروزرسانی نرمافزار.
سایر مشکلات
- تغییر ابعاد محصول نهایی: تغییر ابعاد محصول نهایی میتواند به دلیل سایش غلتکها، تنظیم نادرست سیستم کنترل یا تغییرات در خواص مواد اولیه رخ دهد.
- راه حل: تنظیم دقیق سیستم کنترل، تعویض غلتکهای سایش یافته و بررسی خواص مواد اولیه.
- ایجاد خط و خش روی سطح محصول: ایجاد خط و خش روی سطح محصول میتواند به دلیل وجود ذرات خارجی در سیستم، سایش غلتکها یا تنظیم نادرست نیروی نورد رخ دهد.
- راه حل: تمیز کردن سیستم، تعویض غلتکهای سایش یافته و تنظیم دقیق نیروی نورد.
اینها تنها برخی از مشکلات رایج در دستگاههای نورد هستند و ممکن است مشکلات دیگری نیز رخ دهد. برای تشخیص و رفع مشکلات، بهتر است از متخصصین مجرب نیز کمک بگیرید.
نکات پایانی در مورد دستگاه نورد ورق
همانطور که در این مقاله اشاره شد، نورد، یکی از بهترین روشهای فرمدهی فلزات است و کاربردهای مختلفی دارد. در کل دو نوع عملیات نورد سرد و گرم وجود دارد که هر کدام شرایط خاص خود را دارند. این عملیات با دستگاه نورد انجام میشود. همچنین، دستگاه نورد ورق هم انواع مختلفی دارد که هر کدام از اجزای متفاوتی تشکیل میشوند.
بهطور کلی عملیات نورد مهمترین روش تولید مقاطع فلزی مختلف است و این امکان را دارد قطعاتی با ضخامت بالا را به ورقهایی با کمترین ضخامت تبدیل کند. این عملیات و سایر عملیاتی که در کنار نورد انجام میشوند مانند گالوانیزاسیون، علاوهبر تولید قطعات با ضخامت و طول مختلف، باعث میشوند تا کیفیت محصول نهایی که تولید میشود برای راهاندازی بسیاری از صنایع و ساخت تجهیزات آنها مناسب باشد. ساخت باکیفیت این محصولات باعث میشود محصول نهاییای که از این مقاطع تولید میشود هم دارای کیفیت و دوام مطلوبی باشد.
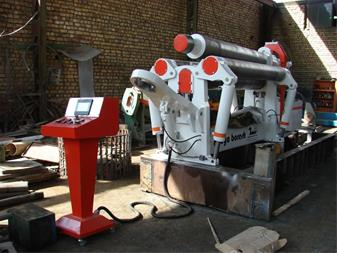
منبع: صبا