عملیات حرارتی فولاد
عملیات حرارتی فولاد فرآیندی حیاتی است که جهت تغییر خواص مکانیکی فولاد به کمک گرمایش و خنک کردن آن، به روشی کنترل شده انجام میشود. به عبارت دیگر علت عملیات حرارتی تغییر خواص مکانیکی فولاد میباشد. این فرآیند برای قرنها انجام شده است و تولید محصولات فولادی را با ایجاد امکان تولید فولاد با سختی، استحکام، چقرمگی و سایر ویژگیهای مطلوب، متحول کرده است. عملیات حرارتی میتواند با قرار دادن فولاد در چرخههای گرمایش و سرمایشی خاص، عملکرد، دوام و مناسب بودن آن را برای کاربردهای مختلف به میزان قابل توجهی بهبود ببخشد. به همین دلیل فولادی که طی فرایند عملیات حرارتی قرار بگیرد قوطی آهن و پروفیل سبک با کیفیتتری را نیز حاصل میشود. نقش حیاتی عملیات حرارتی فولاد در شکلدهی مواد، از صنایع خودروسازی و هوافضا گرفته تا تولید ابزار و قالب، کاملاً مشهود بوده و قابل ستایش است. در این مقاله، مفاهیم، فرآیندها، مزایا، معایب، کاربردها و انواع عملیات حرارتی فولاد را بررسی خواهیم کرد و درک جامعی از این تکنیک اساسی در متالورژی ارائه میکنیم.
تاریخچه عملیات حرارتی فولاد
شروع داستان عملیات حرارتی فولاد به هزاران سال پیش برمیگردد. روزی که تمدنهای باستانی، مانند مصریان و هیتیها، تکنیکهای اولیه عملیات حرارتی را برای بهبود خواص ابزار و سلاحهای خود انجام میدادند. این اتفاق به روال عادی ساخت سلاحها تبدیل شده بود و روشی معمول بود. اما توسعه آن در قرون وسطی و در اروپا شکل گرفت.
قرون وسطی
در اوایل قرون وسطی، آهنگران مشاهده کردند که حرارت دادن فولاد و سرد کردن سریع آن در آب یا روغن، آن را سختتر و بادوامتر میسازد. این تکنیک ابتدایی عصر باستان که امروزه به عنوان کوئنچ شناخته میشود، اساس عملیات حرارتی بود. با گذشت زمان، آهنگران با محیطهای خنک کننده مختلف آزمایش کردند و متوجه شدند که استفاده از مواد مختلف مانند آبنمک یا چربیهای حیوانی میتواند خواص فولاد را تغییر دهد.

دوره رنسانس
در طول دوره رنسانس، تحقیقات علمی و پیشرفت در متالورژی شروع به روشن کردن اصول اساسی عملیات حرارتی فولاد کرد. در این دوره محققانی مانند لئوناردو داوینچی (Leonardo da Vinci) و وانوکچیو بیرینگوچیو (Vannoccio Biringuccio) اثرات گرمایش و سرمایش بر فلزات را مطالعه کرده و زمینه را برای درک علمی این فرآیند فراهم کردند.
عصر مدرن
در قرن 19 و 20، انقلاب صنعتی و توسعه فولاد (به عنوان یک ماده صنعتی عمده) منجر به پیشرفتهای قابل توجهی در فناوری عملیات حرارتی شدند. کشف آلیاژهای جدید و معرفی روشهای گرمایش و سرمایش دقیقتر، مانند کورههای الکتریکی و عملیات حرارتی اتمسفر کنترل شده، امکانات عملیات حرارتی فولاد را بیشتر گسترش داد.
امروزه عملیات حرارتی فولاد با تکنیکها و تجهیزات پیشرفته برای کنترل دقیق خواص مواد به یک زمینه بسیار تخصصی تبدیل شده است. این یک فرآیند ضروری در صنایع مختلف از جمله خودروسازی، هوافضا، ماشینآلات و ساختوساز است که در آن عملکرد اجزای فولادی بسیار مهم است.
توسعه تاریخی عملیات حرارتی فولاد گواهی بر تمایل انسان به بهبود خواص مواد و استفاده از پتانسیل کامل آنهاست. دانش و پیشرفتهای انباشته شده در تکنیکهای عملیات حرارتی نقشی حیاتی در شکلدهی به تولید فولاد مدرن ایفا کرده و به توسعه محصولات فولادی قویتر، بادوامتر و همهکارهتر کمک کرده است.
عملیات حرارتی فولاد چیست و مفاهیم، فرآیندها و انواع آن
عملیات حرارتی (به انگلیسی Heat treatment) فرآیندی حیاتی است که برای اصلاح خواص مواد از طریق گرمایش و سرمایش کنترل شده استفاده میشود. مشخصاً عملیات حرارتی فولاد مخصوص فولاد بوده و فقط به اصلاح خواص این ماده میپردازد. این موضوع شامل چندین مفهوم و فرآیند کلیدی است که برای دستیابی به ویژگی های مواد مورد نظر ضروری هستند. بیایید برخی از مفاهیم و فرآیندهای اساسی عملیات حرارتی را بررسی کنیم:
آنیلینگ
آنیلینگ یک فرآیند عملیات حرارتی است که شامل حرارت دادن فولاد تا دمای خاص، نگه داشتن آن برای مدتی در همان دما و سپس سرد کردن آهسته آن است. به عبارت دیگر بازپخت در عملیات حرارتی همان آنیلینگ است و هدف از بازپخت، نرم کردن فولاد، کاهش تنشهای داخلی، بهبود قابلیت ماشینکاری و اصلاح ساختار دانه است. انواع مختلف آنیلینگ شامل عملیات حرارتی تنشزدایی، بازپخت کامل و بازپخت فرآیندی است که هر کدام از آنها گرمایش و سرمایش خاص خود را شامل میشوند. همچنین در این نوع از عملیات حرارتی ممکن است پرلیت به وجود بیاید که کاربرد اصلی آن در سیم بکسلهای نگهدارنده پلها و سیمهای پیانو میباشد. تشکیل پرلیت در عملیات حرارتی نیز این گونه است که فولاد تا دمای خاصی گرم شده و سپس به آرامی سرد میشود. این خنک شدن آهسته باعث ایجاد پرلیت میشود.
عادی سازی
نرمالیزاسیون یک فرآیند عملیات حرارتی است که شامل حرارت دادن فولاد تا بالاتر از دمای بحرانی و سپس خنک کردن آن میباشد. هدف از نرمالسازی، اصلاح ساختار دانه، افزایش خواص مکانیکی و بهبود قابلیت ماشینکاری است. عادیسازی معمولاً جهت آمادهسازی فولاد برای فرآیندهای عملیات حرارتی بعدی یا دستیابی به ترکیب مطلوبی از استحکام و شکلپذیری استفاده میشود.
کوئنچینگ
عملیات حرارتی کوئنچینگ یک فرآیند خنککننده سرعتی است که شامل گرم کردن فولاد تا دمای خاص و سپس سرد کردن سریع آن با غوطهور کردنش در یک محیط سرد کننده مانند آب، روغن یا محلول پلیمری است. هدف از عملیات حرارتی کوئنچ دستیابی به سختی و استحکام بالا با تغییر ساختارهای ریزساختار فولاد میباشد. انتخاب محیط کوئنچ و سرعت سرد شدن نقش مهمی در تعیین خواص نهایی فولاد دارد.
تمپرینگ
عملیات حرارتی تمپرینگ فرآیندی است که پس از کوئنچینگ انجام میشود. این فرایند شامل حرارت دادن فولاد سرد شده تا دمای خاص و سپس خنک کردن آن میشود. هدف از تمپرینگ، کاهش سختی و شکنندگی ناشی از کوئنچ، کاهش تنشهای پسماند و بهبود چقرمگی و شکلپذیری آن میباشد.همچنین تمپر در عملیات حرارتی باعث دستیابی به تعادل مطلوب بین سختی و چقرمگی در فولاد میشود.
سخت شدن
هاردنینگ یا همان سخت شدن یک فرآیند عملیات حرارتی است که شامل حرارت دادن فولاد تا دمای بالاتر از نقطه بحرانی و سپس سرد کردن سریع آن برای دستیابی به حداکثر سختی و مقاومت در برابر سایش است. این فرایند به طور معمول ساختاری سخت و شکننده ایجاد میکند که اغلب با تمپرینگ برای بهبود چقرمگی دنبال میشود. هاردنینگ معمولاً برای قطعاتی مانند ابزارهای برش و چرخ دندهها که به مقاومت در برابر سایش بالایی نیاز دارند استفاده میشود.
سخت شدن بدنه
کیس هاردنینگ یا همان سخت شدن بدنه یک فرآیند عملیات حرارتی سطحی است که برای افزایش سختی و مقاومت در برابر سایش در لایه بیرونی فولاد و در عین حال حفظ یک هسته سخت و انعطافپذیر استفاده میشود. سخت شدن بدنه شامل وارد کردن کربن یا نیتروژن به سطح فولاد شده که معمولاً از طریق روشهایی مانند کربورسازی یا نیترید کردن انجام میشود. این فرآیند با حفظ خواص مورد نظر هسته، یک لایه سطحی سخت شده ایجاد میکند.
آستمپرینگ
عملیات حرارتی آستمپرینگ شامل حرارت دادن فولاد تا دمایی خاص و سپس نگه داشتن آن در آن دما برای مدت طولانی میباشد. این فرآیند یک ریزساختار منحصر به فرد به نام بینیت تولید میکند که تعادلی از استحکام، چقرمگی و شکلپذیری را فراهم میکند. همچنین آستمپرینگ برای بهبود عملکرد اجزای تحت تاثیر ضربه استفاده میشود.
مارتمپرینگ
Martempering فرآیندی شبیه به آستمپرینگ است که شامل حرارت دادن فولاد تا دمای بالاتر و سپس سرد کردن سریع آن برای رسیدن به یک ساختار مارتنزیتی میباشد. مارتمپرینگ در حالی که ترکیبی از استحکام و چقرمگی را فراهم کرده خطر اعوجاج و ترک خوردن ناشی از سرد شدن را کاهش میدهد.
ساب زیرو
عملیات حرارتی زیر صفر شامل قرار دادن مواد در معرض دمای بسیار پایین، (که معمولاً زیر 100- درجه سانتیگراد است) در مدت زمانی طولانی میشود. در طی این عملیات، مواد به تدریج تا دمای مورد نظر خنک میشوند. سپس برای چندین ساعت در آن دما نگه داشته شده و به آرامی به دمای اتاق باز می گردند. عملیات حرارتی ساب زیرو (Subzero) در صنایع مختلفی از جمله خودروسازی، هوافضا، تولید ابزار و کارد و چنگال نیز کاربرد دارد.
عملیات حرارتی به روش القایی
سخت کاری القایی، یک فرآیند عملیات حرارتی تخصصی است که از القای الکترومغناطیسی برای گرم کردن سطح یا نواحی موضعی قطعه کار استفاده میکند. معمولاً برای عملیات حرارتی روی فلزات استفاده شده و مزایای متعددی نسبت به روشهای عملیات حرارتی سنتی دارد. اما برای برخی از انوع فولاد هم کاربرد داشته و تنها مخصوص فلزات نیست.
عملیات حرارتی همگن
عملیات حرارتی همگن، یک فرآیند عملیات حرارتی است که هدف آن دستیابی به خواص مواد ثابت و یکنواخت در کل حجم قطعه کار است. تفاوت اصلی این روش با عملیات حرارتیهای دیگر این است که کل قطعه کار را به طور همزمان گرم کرده و تمام سطوح را مورد هدف قرار میدهد.
اینها تنها چند نمونه از انواع فرآیندهای عملیات حرارتی مورد استفاده در تولید فولاد بوده و موارد زیادی از قبیل عملیات حرارتی پیرسختی و عملیات حرارتی تحت خلا وجود دارند که ذکر همه آنها در این مقاله نمیگنجد. انتخاب فرآیند عملیات حرارتی مناسب به عواملی مانند خواص مورد نظر، ترکیب فولاد، هندسه اجزا و الزامات کاربرد بستگی دارد. هر فرآیند دارای مزایای منحصر به فردی از نظر اصلاح خواص فولاد است که هر کدام برای کاربردی خاص استفاده میشود.
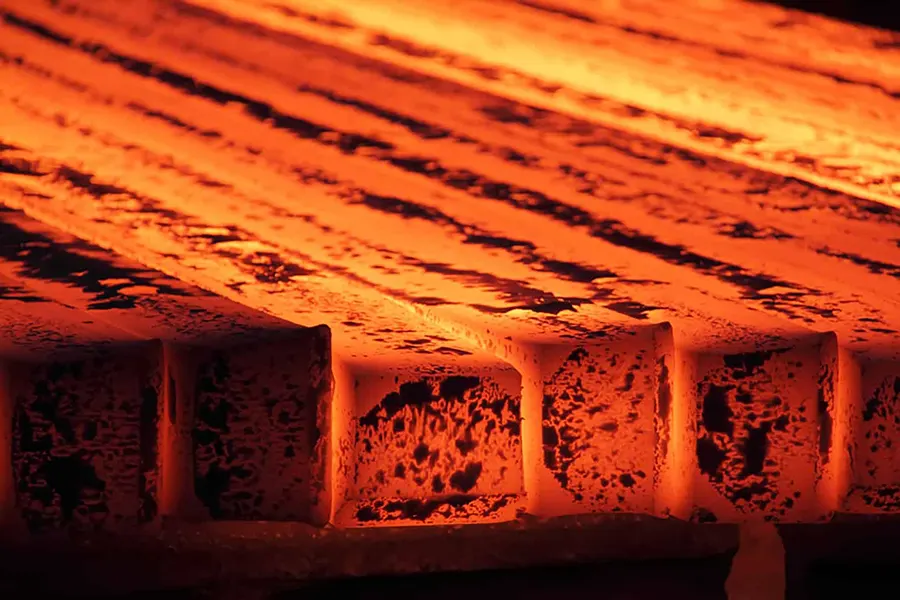
مزایای عملیات حرارتی فولاد
عملیات حرارتی فولاد دارای چندین مزیت است که این مزیتها آن را به یک فرآیند ارزشمند در صنایع مختلف تبدیل میکند. برخی از مزایای کلیدی عملیات حرارتی فولاد عبارتند از:
1. افزایش سختی
برخی از فرایندهای عملیات حرارتی از قبیل کوئنچینگ و هاردنینگ (سخت شدن) باعث بالا رفت سختی فولاد به میزان قابل توجهی میشوند. این موضوع باعث شده تا فولاد برای استفاده در قطعاتی مثل ابزارهای برش، چرخ دنده و یاتاقان که نیاز به مقاومت در برابر فشار دارند مناسب شود.
2. تقویت استحکام فولاد
بالا رفتن استحکام فولاد با اصلاح ریزساختارهای آن یکی از مزیتهای عملیات حرارتی است. این اتفاق با عملیاتهایی مثل تمپرینگ و کوئنچینگ قابل انجام بوده و باعث تحملپذیری فولاد در مقابل تنشها و بارهای سنگین میشود.
3. بهبود چقرمگی
عملیات حرارتی میتواند چقرمگی فولاد را بهبود بخشیده و آن را در برابر بارهای ضربهای و شکستن مقاومتر کند. این اتفاق توسط فرآیندهایی مانند تمپرینگ رخ میدهد که به تعادل میان سختی و انعطافپذیری کمک کرده و باعث افزایش مقاومت در مقابل ترکخوردگی میشود.
4. تقویت شکلپذیری
بسته به فرآیند عملیات حرارتی خاص به کار رفته، فولاد را میتوان کم و بیش انعطافپذیر ساخت. اما به طور خاص عملیات بازپخت یا همان آنیل کردن فولاد را نرم کرده و شکلپذیری آن را تقویت میکند. این موضوع باعث آسان شدن شکلدهی و تغییر شکل فولاد شده و آن را برای صنایعی که نیاز به شکلپذیری فولاد دارند مناسب میکند.
5. تساهل ماشینکاری
عملیات حرارتی میتواند ماشینکاری و ساخت فولادها را آسانتر کند. این موضوع از طریق فرآیندهایی مثل بازپخت و عادیسازی قابل انجام است که باعث کاهش تنشهای داخلی فولاد و ساییدگی ابزار شده و افزایش سرعت برش را حاصل میشود.
6. شخصیسازی خواص
یکی از مزایای قابل توجه عملیات حرارتی فولاد، توانایی تطبیق خواص مواد با نیازهای کاربردی خاص است. مهندسان با کنترل دقیق پارامترهای گرمایش و سرمایش میتوانند به ترکیب مطلوبی از سختی، استحکام، چقرمگی و شکلپذیری در فولاد دست یابند.
7. افزایش مقاومت در برابر سایش
فرآیندهای عملیات حرارتیای مثل عملیات سخت شدن بدنه، که یک لایه بیرونی سخت شده را بر روی سطح فولاد تشکیل میدهند، به طور قابل توجهی مقاومت اجزای فولادی را دربرابر سایش بهبود میبخشند. این موضوع باعث میشود تا فولاد در کاربردهایی که در معرض اصطکاک، سایش یا تماس لغزشی قرار میگیرد کارایی داشته باشد. به عنوان مثال قطعاتی مانند چرخ دندهها، میل بادامک و اجزای موتور که در معرض سایش قرار دارند با این روش تولید میشوند.
8. پایداری ابعادی
عملیات حرارتی میتواند باعث بهبود ثبات ابعادی فولاد شده و اعوجاج و تاب برداشتن را در حین ماشینکاری به حداقل برساند. بنابراین با کاهش تنشهای داخلی و کنترل فرآیند خنک سازی، شکل و ابعاد اجزای فولادی عملیات حرارتی شده با دقت بیشتری حفظ میشود.
9. تطبیقپذیری
عملیات حرارتی فولاد یک فرآیند همه کاره است که میتواند برای انواع مختلف آلیاژهای فولادی از جمله فولادهای کربنی، فولادهای آلیاژی و فولادهای ابزاری اعمال شود. همچنین میتوان آن را متناسب با ضخامتها، شکلها و اندازههای مختلف مواد تطبیق داد که این موضوع فولاد را برای طیف گستردهای از کاربردهای صنعتی قابل استفاده میکند.
به طور کلی، عملیات حرارتی فولاد مزایای متعددی را ارائه میدهد که خواص مکانیکی، دوام و عملکرد اجزای فولادی را افزایش داده و آن را به یک فرآیند ضروری در صنایعی مانند خودروسازی، هوافضا و ساختمانسازی تبدیل میکند.
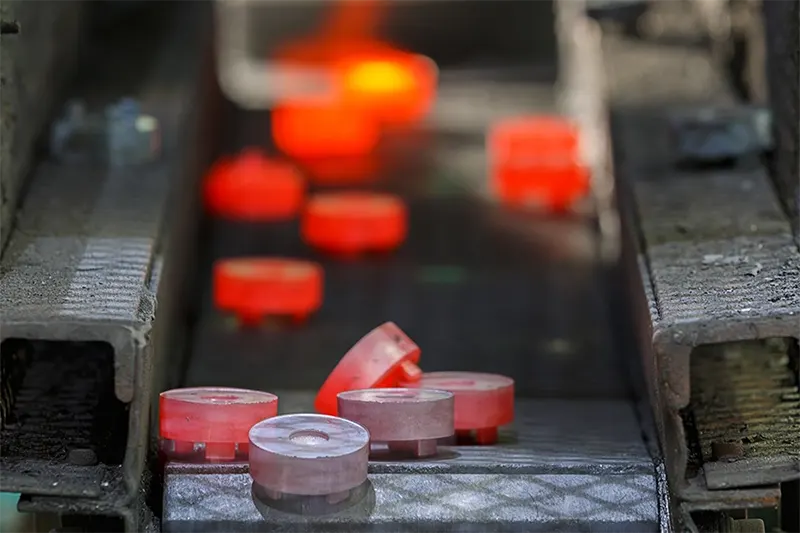
معایب عملیات حرارتی فولاد
در حالی که عملیات حرارتی فولاد مزایای قابل توجهی را ارائه میدهد، معایب و محدودیتهایی هم دارد که باید آنها را مورد توجه قرار دهیم. برخی از معایب کلیدی عملیات حرارتی فولاد عبارتند از:
1. اعوجاج و تاب برداشتن
عملیات حرارتی به معنی قرار دادن فولاد در دمای بالا و سپس سرد کردن آن با سرعتهای متفاوت است. این چرخههای حرارتی میتوانند باعث ایجاد اعوجاج در مواد و تاب برداشتن آنها شده و شکل و ابعادشان را تغییر دهند.
2. خطر ترک خوردگی
روشهای عملیات حرارتی نامناسب یا سرعت خنکسازی سریع میتواند منجر به تنشهای حرارتیای شود که خارج از توان مقاومتی فولاد بوده و باعث ترک خوردن آن میشود. خطر ترک خوردن در فولادهایی با محتوای کربن بالاتر یا در فولادهایی که مستعد تشکیل فازهای شکننده در طول خنک شدن هستند، بیشتر است. برای به حداقل رساندن احتمال ترک خوردگی بسیار مهم است که کنترل فرآیند مناسبی انجام شده و سرعت خنک شدن درستی انتخاب شود.
3. پیچیدگی و مهارت مورد نیاز
عملیات حرارتی فولاد، فرآیند پیچیدهای است که نیاز به تخصص و کنترل دقیق بر پارامترهای مختلفی مانند دمای گرمایش، زمان خیساندن، نرخ خنک کننده و شرایط دمپر دارد. دستیابی به خواص مطلوب در عین پرهیز از اثرات نامطلوب نیازمند دانش، تجربه و مهارت بالایی میباشد و نباید توسط افراد کم مهارت انجام شود.
4. کاربرد محدود برای برخی از فولادها
برخی از آلیاژهای فولادی ممکن است به دلیل ترکیب یا ویژگیهای ریزساختاریای که دارند برای فرآیندهای عملیات حرارتی خاص مناسب نباشند. به عنوان مثال، برخی از فولادهای ضد زنگ سختیپذیری خوبی ندارند و ممکن است به روشهای جایگزین برای تقویت سختی نیاز داشته باشند.
5. کربن زدایی سطحی
در طی فرآیندهای عملیات حرارتیای که شامل دماهای بالا میشوند، ممکن است سطوح فولادی دچار کربن زدایی شوند که باعث از دست رفتن محتوای کربن آنها میشود. این موضوع میتواند بر سختی سطح و مقاومت در برابر سایش فولاد تأثیر منفی گذاشته و نیاز به عملیات سطحی اضافه یا کنترل دقیق عملیات حرارتی برای به حداقل رساندن این اثر داشته باشد.
6. مصرف انرژی
فرآیندهای عملیات حرارتی فولاد معمولاً شامل حرارت دادن فولاد تا دمای بالا و برای دورههای طولانی بوده که انرژی قابل توجهی را مصرف میکنند. این موضوع میتواند باعث ایجاد اثرات زیست محیطی مخربی شود. مخصوصاً اگر برای این کار از روشهای گرمایش یا سرمایش ناکارآمدی استفاده شده باشد.
7. زمان و هزینه فرآیند
عملیات حرارتی یک مرحله اضافی در فرآیند تولید است که زمان و هزینهای را به کل تولید اضافه میکند. همچنین برای اطمینان از دستیابی به نتایج مطلوب، به تجهیزات تخصصی، پرسنل ماهر و نظارت دقیق نیاز میباشد. افزایش زمان پردازش و هزینههای مربوطه را باید با مزایای به دست آمده از خواص فولاد عملیات حرارتی شده سنجید تا سود و زیان آن مشخص شود.
8. کنترل محدود بر ریزساختار
در حالی که عملیات حرارتی میتواند ریزساختار فولاد را اصلاح کند، محدودیتهایی برای میزان کنترل آن وجود دارد. عواملی مانند ترکیب فولاد، سوابق پردازش و سرعت خنکسازی میتوانند بر ریزساختار نهایی تأثیر بگذارند.
علیرغم این محدودیتها، مزایای عملیات حرارتی فولاد اغلب از معایب آن بیشتر بوده و در عین حال با کنترل صحیح فرآیند میتوان به کاهش مشکلات احتمالی و افزایش مزایای آن کمک کرد.
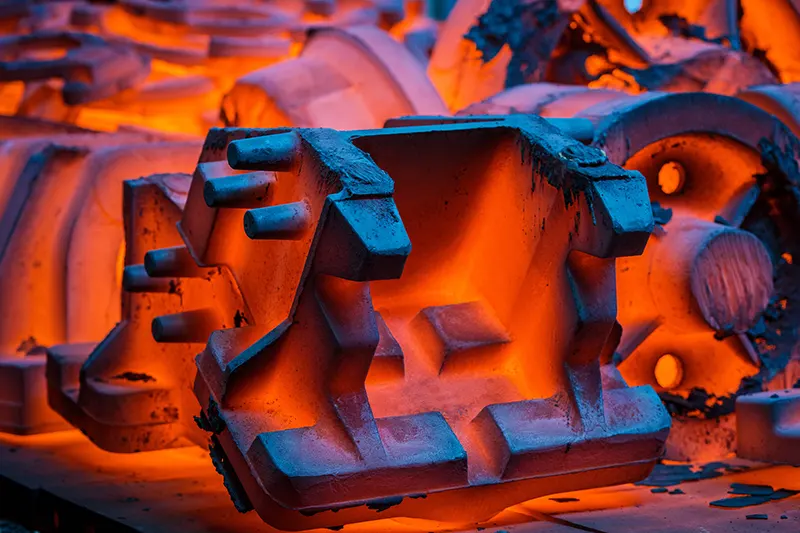
کاربردهای فولاد عملیات حرارتی شده
فولاد عملیات حرارتی شده به دلیل خواص و عملکرد بهبود یافتهای که دارد در صنایع مختلف کاربرد گستردهای پیدا کرده است. برخی از کاربردهای فولاد عملیات حرارتی شده عبارتند از:
- ساخت قطعات حیاتی مانند میل لنگ، میل بادامک، چرخدندهها، محورها و اجزای انتقال در صنعت خودرو
- تولید ارابههای فرود هواپیما، دیسکهای توربین، اجزای موتور و قطعات ساختاری مورد استفاده در صنایع هوافضا
- تولید ابزارهای برش، قالبها و پانچها
- ساخت میلگردهای تقویتکننده، اجزای سازهای فولادی و پیچهای لنگر مورد استفاده در ساختمانها، پلها و سایر پروژههای زیربنایی
- تولید لولههای حفاری، دریچهها، سرچاهها و ابزارهای حفاری مورد استفاده در صنعت نفت و گاز
- تولید پرههای توربین، اجزای ژنراتور و قطعات دیگ بخار مورد استفاده در صنعت برق
- تولید قطعات ماشین آلات و تجهیزاتی مانند چرخ دندهها، شفتها، یاتاقانها و فنرها
- ساخت ابزار و ایمپلنتهای پزشکی
این موارد تنها چند نمونه از کاربردهای فولاد عملیات حرارتی شده در صنایع مختلف بودند. چرا که فرآیندها و پارامترهای عملیات حرارتی برای برآورده کردن نیازهای منحصر به فرد هر صنعت طراحی شدهاند و عملکرد و دوام اجزای فولادی را تضمین میکنند. به عبارت دیگر طراحی عملیات حرارتی به منظور رفع نیاز در صنایع مختلف انجام پذیرفته و صنایع زیادی را دربرمیگیرد.
جمعبندی
عملیات حرارتی به زبان ساده یک فرآیند حیاتی برای افزایش خواص مواد میباشد. این فرایند، مزایایی مانند سختی، استحکام، چقرمگی و مقاومت در برابر سایش را ارائه میدهد و در عین حال ممکن است مشکلاتی مانند ایجاد اعوجاج و افزایش هزینههای تولید را به وجود بیاورد. تمام مزایای گفته شده درمورد عملیات حرارتی برای استفاده در صنایعی مانند صنایع خودروسازی، هوافضا، ماشینآلات، ساختمانسازی و غیره بوده و کاربرد فراوانی در صنایع مختلف دارد. در دسترس بودن تکنیکهای مختلف عملیات حرارتی، انعطافپذیری را برای تطبیق خواص مواد با نیازهای کاربردی خاص فراهم کرده و ادامه تحقیقات در این فناوری به توسعه و بهینهسازی فولاد عملیات حرارتی شده کمک میکند.
پرسش و پاسخ
عملیات حرارتی استنلس استیل چیست؟
عملیات حرارتی فولاد ضد زنگ شامل طیف وسیعی از فرآیندها است که هدف آن اصلاح ریزساختار و خواص مواد است. فولاد ضد زنگ به مقاومت در برابر خوردگی، استحکام بالا و دوام زیاد شناخته شده است. با این حال، میتوان از طریق عملیات حرارتی ویژگیهای فولاد را افزایش داده و یا تنظیم کرد. برخی از فرآیندهای معمول عملیات حرارتی برای فولاد ضد زنگ عبارتند از: عملیات حرارتی و تنش زدایی، بازپخت، کوئنچینگ، تمپرینگ و سخت شدن رسوبی.
آیا فلزاتی غیر از آهن و فولاد هم عملیات حرارتی دارد؟
بله. عملیات حرارتی فلزات غیر آهنی شامل تغییر خواص فلزاتی غیر از آهن یا فولاد میباشد که از طریق گرمایش و سرمایش کنترلشده انجام میشود. این عملیاتها شامل عملیات حرارتی آلومینیوم، برنج، برنز، تیتانیوم، نیکل و بسیاری دیگر از فلزات میشوند. یکی از عملیات حرارتیهای رایج در میان فلزات غیر آهنی عملیات حرارتی مس و آلیاژهای آن است که در قطعات الکتریکی و الکترونیکی، مبدلهای حرارتی، صنعت خودرو، ضرب سکههای مسی و صنایع هوافضا کاربرد دارد.
عملیات حرارتی پیشگرم و پسگرم چیست؟
عملیات حرارتی پیشگرم و پسگرم دو فرآیند تکمیلی هستند که اغلب در حین یا بعد از فرآیند جوشکاری انجام میشوند. به همین دلیل به آنها عملیات حرارتی بعد از جوشکاری هم میگویند. هدف این عملیات حرارتی، کاهش خطر ترکخوردگی، بهبود کیفیت جوش و کاهش تنشهای باقیمانده در اتصال جوش داده شده میباشد.
عملیات حرارتی حجمی چیست؟
همان عملیات حرارتی همگن است که به این نام نیز خوانده میشود.
منبع: فولاد صبا