بهینهسازی کوره فولادسازی با ترکیب CBIC و CDRI
در حال حاضر، در برخی مناطق جهان، محصولات آهن اسفنجی (DRI) سهم قابل توجهی از بار فلزی کورههای فولادسازی با تکنولوژیهای الکتریکی را تشکیل میدهند. به طور خاص، کشورهای هند و ایران به دلیل برخورداری از مزایای نسبی در زمینه مواد اولیه و حاملهای انرژی، هر ساله حجم زیادی از آهن اسفنجی تولید میکنند؛ به طوری که این محصولات، بخش عمدهای از بار فلزی کورههای فولادسازی الکتریکی (بین70 تا95 درصد) را شامل میشوند. به عبارت دیگر، آهن اسفنجی به خاطر ویژگیهای فیزیکی و شیمیایی یکنواخت خود و غلظت پایین عناصر ناخالصی، موفق به کسب جایگاهی در سبد شارژ کورههای فولادسازی الکتریکی بسیاری از فولادسازان شده است. پیشبینیهای بینالمللی نشان میدهند که تا افق2040، تقاضای جهانی برای محصولات خانواده آهن اسفنجی به بیش از250 میلیون تن خواهد رسید، در حالی که تولید جهانی این محصولات در سال2021 حدود120 میلیون تن بوده است.
اگر محصولات آهن اسفنجی به عنوان شارژ اصلی در کورههای الکتریکی به کار روند، به دلیل تفاوت خواص آنها با قراضه، اصلاحاتی در نظام شارژ کوره و تغییراتی در عملکرد و پارامترهای عملیاتی آن اجتنابناپذیر خواهد بود. از جمله اصلیترین تغییراتی که در پارامترهای عملیاتی کوره روی خواهد داد میتوان به جایگزینی تغذیه مداوم آهن اسفنجی به جای تغذیه منقطع قراضه، تغییر در میزان مواد شارژ شده به کوره (از قبیل کربن، آهک، اکسیژن و …) و همچنین تغییر در مصرف انرژی و زمان تخلیه (tap to tap) اشاره کرد.
دو عامل “میزان نرمه همراه” و “درجه فلزی” در عملکرد فولادسازی محصولات خانواده آهن اسفنجی تأثیر بسزایی دارند. در ارتباط با “نرمه” (حجم کمتر از6 میلیمتر)، باید گفت که هرچه میزان نرمه در محصول کمتر باشد، تلفات آهن در فرآیند فولادسازی کاهش مییابد. به همین دلیل، اکثریت فولادسازان پیش از شارژ محصول آهن اسفنجی سرد (CDRI) به کوره، اقدام به غربال کردن آن و جداسازی نرمه از محصول اصلی میکنند. با این حال، با عرضه محصول CBIC که نرمه کمتری نسبت به CDRI دارد، مشکل جدایش نرمه از محصول برطرف شده است.
از سوی دیگر، همانطور که اشاره شد، مقاومت بالاتر CBIC در برابر اکسیداسیون نسبت به CDRI باعث میشود که افت درجه فلزی محصول در حین ذخیرهسازی و حمل کمتر باشد، که این امر مزایای زیادی برای فرآیند فولادسازی به همراه دارد. در شکل زیر نشان داده شده است که کاهش درجه فلزی آهن اسفنجی در کوره فولادسازی منجر به افزایش مصرف انرژی الکتریکی، نسوز و الکترود گرافیتی میشود و در نتیجه به کاهش راندمان و توان تولید میانجامد. بر اساس گزارشهای دریافتی از هزینههای تولید فولاد در واحدهای فولادسازی داخلی، میتوان برآورد کرد که کاهش هر1 درصدی در درجه فلزی محصول باعث افزایش حدود2 درصدی هزینه تبدیل آهن اسفنجی به شمش فولادی خواهد شد که تأثیرات چشمگیری بر شاخصهای اقتصادی واحدهای فولادسازی دارد.
مزیت دیگری که با بریکتسازی آهن اسفنجی در کوره فولادسازی حاصل میشود، افزایش سرعت عبور بریکت از سرباره مذاب نسبت به آهن اسفنجی است. این امر به دلیل دانسیته بالاتر بریکت بوده و میتواند موجب کاهش تلفات ناشی از سوختن آهن اسفنجی، تسریع در فرآیند فولادسازی و بهبود راندمان تولید گردد.
یکی دیگر از ویژگیهای کلیدی محصول CBIC که در دیگر محصولات خانواده آهن اسفنجی مشاهده نمیشود، قابلیت تنظیم کربن محتوی آن است. این ویژگی بهطور قابل توجهی نیاز به شارژ دستی کربن به کوره فولادسازی – که معمولاً از راندمان پایینی برخوردار بوده و همراه با تلفات قابل توجهی است – را از میان برده و بهبود میبخشد.
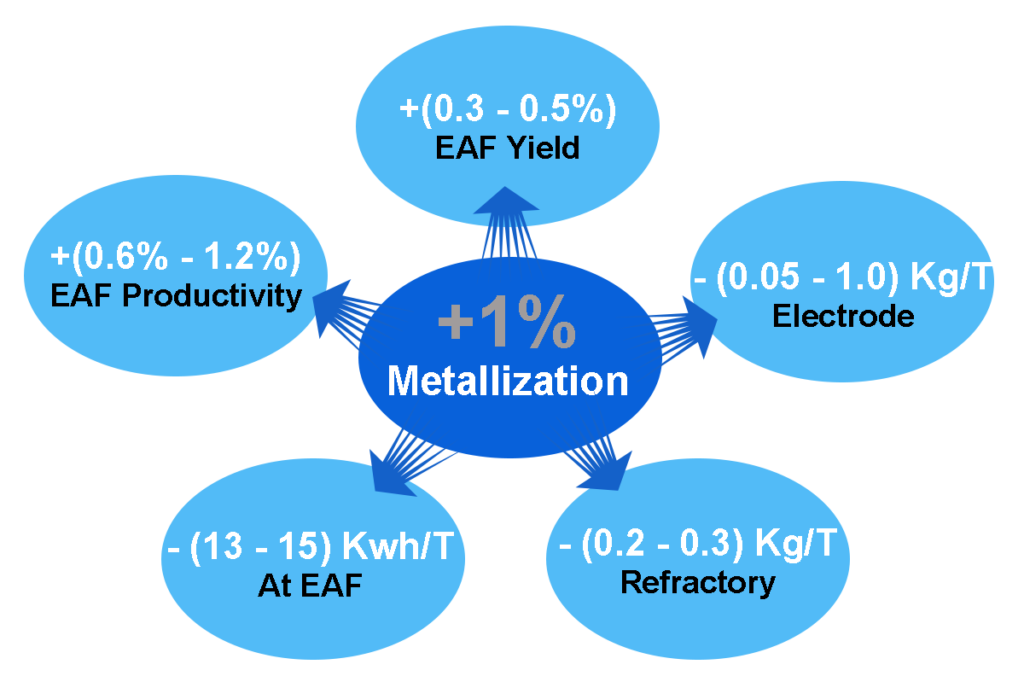
بررسیهای انجامشده در زمینه مقایسه رفتار فولادسازی CBIC و CDRI نشان میدهد که شارژ ترکیبی این دو محصول به کوره فولادسازی بهترین نتایج را به دنبال دارد. بهطوریکه میتوان از مزایای هر دو محصول به طور همزمان بهرهمند شد. نتایج نشان میدهد افزایش هر10 درصدی CBIC در شارژ کوره فولادسازی باعث کاهش2 درصدی در مصرف انرژی الکتریکی،1.7 درصدی در زمان ذوب و0.5 درصدی در راندمان تولید فولاد میگردد.علاوه بر این، با افزایش میزان CBIC در رژیم شارژ کوره، میزان غبار تولید شده در طول فرآیند فولادسازی بهطور قابل توجهی کاهش مییابد، که این ناشی از استحکام مکانیکی و مقاومت بالای این محصول نسبت به CDRI است. در نهایت، نتایج نشان میدهد که حضور30 تا40 درصدی CBIC در رژیم شارژ کوره، بهترین نتایج را در فرایند فولادسازی به همراه خواهد داشت.