استفاده از بریکت آهن اسفنجی در فرآیند کوره بلند-کنورتور
در سالهای اخیر، سازمان بهداشت جهانی (WHO) توجه خاصی به صنایع آلاینده در سطح جهانی داشته است. این سازمان از طریق ابراز نگرانیهای مختلف، روند فزاینده آلودگی هوا و تأثیر صنایع آلاینده بر انتشار گازهای گلخانهای و گرمایش جهانی را مورد توجه قرار داده است. بهطوریکه در سال2015، مجمع بینالمللی تغییرات آب و هوایی (IPCC) گزارش داد که بیش از20 درصد گازهای گلخانهای تولیدشده در سطح جهان به صنایع مربوط میشود و از بین این صنایع، صنعت آهن و فولاد حدود35 درصد را به خود اختصاص داده است. در این صنعت، واحدهای آهنسازی کوره بلند به دلیل استفاده از کک، تقریباً80 درصد از کل CO2 تولیدی در این حوزه را ایجاد میکنند.
با توجه به آمارهای جهانی درباره مصرف زغالسنگ در صنعت آهن و فولاد، میزان CO2 تولیدی در واحدهای کوره بلند تقریباً1.8 تن به ازای هر تن آهن خام تولیدی تخمین زده میشود. در عوض، واحدهای احیای مستقیم پایه-گاز به میزان35 درصد از حجم آلایندههای تولیدی در واحدهای کوره بلند اشاره شدهاند. به این ترتیب، در حال حاضر فرآیندهای آهنسازی بر پایه احیای مستقیم بهعنوان یک روش موثر برای کاهش آلایندههای زیستمحیطی و حفظ فعالیت مجتمعهای فولادسازی مبتنی بر کوره بلند-کنورتور شناخته میشوند. به عبارتی دیگر، استفاده از محصولات آهن اسفنجی در فرآیند فولادسازی کوره بلند-کنورتور بهعنوان یکی از راهکارهای کلیدی برای کاهش مشکلات زیستمحیطی و حفظ جایگاه این فرآیند در سطح جهانی در نظر گرفته میشود.
در فرآیند آهنسازی کوره بلند، معمولاً از موادی چون سنگ آهن درشت دانه، گندله سنگ آهن و آگلومره بهعنوان ورودیهای آهندار به کوره استفاده میشود. تحقیقات نشان میدهد که اگر تمام مواد آهندار شارژ شده به کوره بلند از نوع اکسیدی باشند،45 درصد از کل انرژی مصرفی فرآیند صرف واکنشهای احیاء میشود. از این رو، با جایگزینی بخشی از سنگ آهن با DRI (آهن احیاء شده)، میزان اکسید آهنی که باید در کوره احیاء شود، کاهش مییابد. این تغییر نه تنها باعث کاهش مصرف کک در طی فرآیند میشود، بلکه توان تولید کوره را نیز افزایش میدهد. از دهه80 میلادی تاکنون، مطالعات متعددی در زمینه تأثیر شارژ محصولات DRI به کوره بلند انجام شده و در حال حاضر، بسیاری از فولادسازان در جهان، به ویژه در ایالات متحده، اروپا و ژاپن، بهطور فزایندهای از این محصولات در کورههای خود استفاده میکنند. بر اساس گزارشها، اگر هر10 درصد از آهن ورودی به کوره از نوع آهن احیاء شده باشد، میزان مصرف کک و CO2 تولیدی حدود5 تا7 درصد کاهش یافته و توان تولید حدود6 تا10 درصد افزایش خواهد یافت.
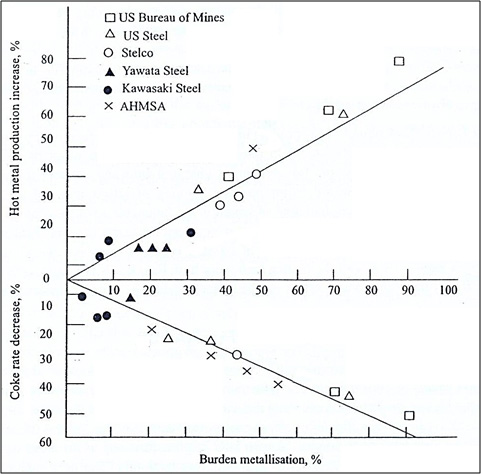
نکتهای که در استفاده از محصولات DRI در کوره بلند باید مورد توجه قرار گیرد، ابعاد و استحکام خردایش (Crush Strength) آنهاست. تحقیقات نشان میدهد که هرچه درصد بیشتری از مواد شارژ شده دارای ابعادی در محدوده15 تا40 میلیمتر و استحکام خردایش بالاتری باشند، نفوذپذیری گاز از بستر مواد بیشتر شده و احتمال خردایش آنها در اثر فشار ستون مواد کاهش مییابد. در این راستا، بریکت داغ آهن اسفنجی (HBI) بهسبب داشتن ابعاد مناسب و استحکام خردایش بالاتر نسبت به آهن احیاء شده مرطوب (CDRI) در بسیاری از کورههای بلند جهان مورد استفاده بیشتری قرار میگیرد.
با توجه به این ویژگیهای بهتر HBI، پیشبینی میشود که در دو دهه آینده، افزایش استفاده از محصولات DRI، به ویژه بریکت DRI در کورههای بلند، ادامه یابد. محدودیتهای زیستمحیطی سختگیرانه برای واحدهای فولادسازی کوره بلند-کنورتور نیز نشاندهنده این است که حرکت این واحدها به سمت تغییر رژیم شارژ کوره و استفاده از بریکت آهن اسفنجی امری اجتنابناپذیر خواهد بود.
به همین دلیل، نیاز جهانی به بریکت آهن اسفنجی در سالهای آتی، بهصورتی خواهد بود که برخی از واحدهای موجود ممکن است نتوانند به تنهایی این نیازها را تأمین کنند. بنابراین، توسعه ظرفیتهای تولید بریکت آهن اسفنجی در مناطق دارای مزایای نسبی، از نظر اقتصادی و منطقی خواهد بود.در این راستا، کشور ایران با تکیه بر واحدهای احیای مستقیم موجود و استفاده از تکنولوژی بومی بریکتسازی سرد، میتواند نقشی تأثیرگذار در آینده بازار جهانی بریکت آهن اسفنجی ایفا کند و با تحولات جهانی در زمینه تغییر رژیم شارژ کوره بلند-کنورتور همسو شود. این ساختارها میتوانند به بهبود وضعیت بازار و تأمین نیازهای رو به رشد جهانی در این حوزه کمک کنند.